Cone Mill for Size Reduction
Increase productivity and improve production versatility and reliability across a wide array of dry milling and wet conditioning applications with conical milling.
Cone milling is one of the most common methods of milling in the pharmaceutical, food, chemical and associated industries. They are typically used for size reduction and deagglomeration or delumping of powders and granules.
Generally used for reducing material to a particle size as low as 180µm (80 mesh) a cone mill produces less dust and heat than alternative forms of milling. The gentle grinding action and quick discharge of correctly sized particles ensure tight particle size distributions (PSDs) are achieved.
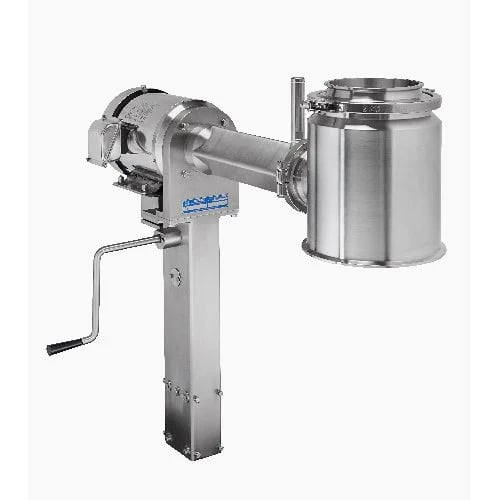
Reassuring Milling Experience
Quadro Engineering invented the original cone or conical mill in 1976. Though simple in principle, the Comil® was a revolutionary concept that has since evolved into a global processing standard adopted by market leaders around the world.
The Cone Mill is typically used for some of the following common applications:
- Sizing wet granulated particles before drying
- Sizing dry granules before the tableting stage
- Delumping dry detergent during production
- Deagglomerating dried fruits - raisins, cranberries
- Reclaiming - broken tablets, broken biscuits are ground back into their powder form before being re-formed
Conical Milling - How it Works
How using a Cone Mill is the right choice for your application.
The Comil® comprises a vertically mounted rotating impeller which moves material across a mill screen causing a low velocity cutting action on the particle. If the particle is the right size it will pass through the screen, if not it remains in the cutting chamber until it reaches the desired size.
Material is fed by gravity into the top of the mill head. It successfully reduces the generation of fines, which mitigates the risk of potential dust explosion hazards.
Keeping it Low
Its low RPM, low-energy, low-heat and low-noise design make it ideal for pharmaceutical particle size reduction applications. The ability to flood feed results in low dust and high throughput.
Tight particle sizing also helps improve the flowability and uniformity of powders before they enter the tablet press.
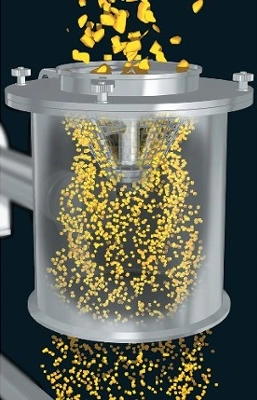
How to Select the Right Milling Equipment
Particle size reduction can be accomplished in a variety of ways
At Quadro Engineering we have a range of mill sizes and configurations, from Lab scale to full-size high-capacity milling machines with Overdriven and Underdriven style models.
The way in which the mill head is mounted can be adjusted to suit the manufacturing needs and application, whether that is on a mobile lifter frame or wall-mounted within the process equipment design. In addition, our High Energy H20 Comil® and the Fine Grind F10 can extend the particle size reduction levels.
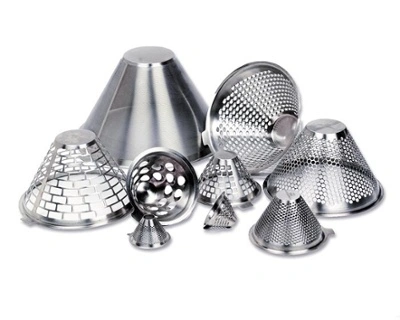
Selecting the right mill for you
Based on your application and material properties (particle size, moisture content, temperature sensitivity, hardness and other physical and chemical properties), we can evaluate your needs and recommend the equipment and process that most efficiently and effectively achieves your specific size-reduction requirements. With a plethora of screens and impellers in our design archives, we will have the right solution for you.