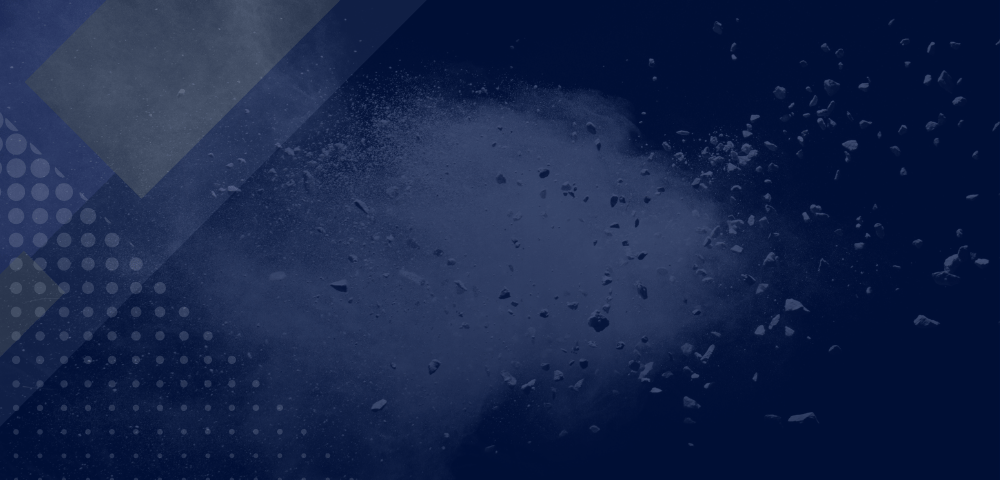
Pharmaceutical Manufacturing Processes
Wet Granulation
Discover the essential steps and equipment for effective wet granulation in pharmaceutical manufacturing.
15 Min Read Time
PROCESS OVERVIEW
The Wet Granulation Process Steps
Wet Granulation is selected as the manufacturing process when the Oral Solid Dosage (OSD) pharmaceutical powders possess poor compressibility. It is the most commonly used production method for Pharmaceutical OSD products as it suits most types of powders (whether they have high or low flowability properties) and has been proven over time to be highly successful.
For decades Quadro has been helping customers around the world optimize their Wet Granulation processes adding value at 3 key stages:
1 – Pre-conditioning powders with screening, delumping or milling.
2 – Wet milling after the high shear granulator.
3 – Dry milling after the fluid bed dryer.
All these steps are designed to condition the pharmaceutical powders so that they create tablets/capsules/sachets that are consistent in weight, contain the target % of API & excipient in each dose, don’t degrade with handling and have the correct bioavailability for a therapeutic dose.
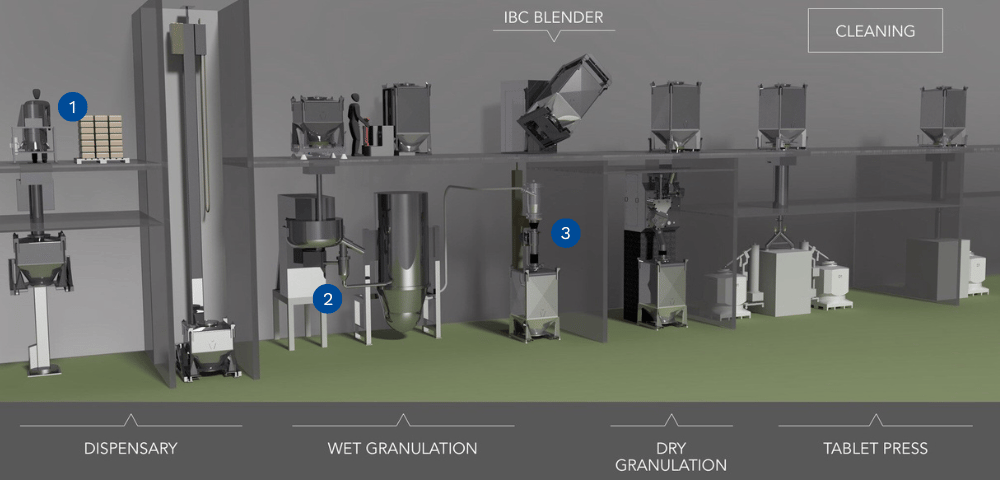
When the original powdered ingredients for the pharmaceutical batch arrive at the manufacturing facility, many of them may have agglomerated and created pellets or lumps in the powder.
As a pre-step, these powders are conditioned to become more free-flowing, removing the lumps and creating the target particle size distribution (PSD) required by the formulation.
This can be achieved in a number of ways depending on the state of the powder:
- Delumping can be done with a Quadro® FlexSift for powders that have easily breakable lumps. Concurrently, the FlexSift provides added security screening to catch any trapped materials in the incoming batch of ingredients.
- For harder lumps in powders, the Quadro® Comil® with a large holed screen and slow impeller speed can be used for deagglomeration.
- To achieve target PSDs, the Quadro® Comil® is often used for Milling of APIs and excipients which will also improve the blend homogeneity and powder flow. If required due to stringent OEB requirements, this can be done in an Isolator to ensure operator safety and/or to retain product integrity.
The Quadro Solution
The Quadro® FlexSift offers enhanced security screening efficiency for greater production output. This provides a major boost in production throughput, achieving higher output and elevating efficiency across the manufacturing process.
High product recovery and reduced cleaning are achieved thanks to its innovative internal structure, the FlexSift boasts impressive recovery rates, ensuring virtually all the material undergoes processing. This efficiency translates into significant cost savings, minimized material wastage, and reduced cleaning intervals – all of which substantially elevate productivity levels.
The Quadro® Comil® provides increased size reduction versatility from its vast array of screen and impeller options, resulting in the ability to achieve target PSDs more easily.
Low-energy milling and high throughput are achieved. Comil’s screen and impeller designs (commonly referred to as ‘tooling’) translate into a gentle size reduction process that minimizes unwanted heat generation while concurrently achieving desired milling results. The same tooling design features that help control milling temperatures result in high throughputs, thus helping to improve processing efficiencies.
Learn more about Screening, Delumping and Milling in the Wet Granulation process.
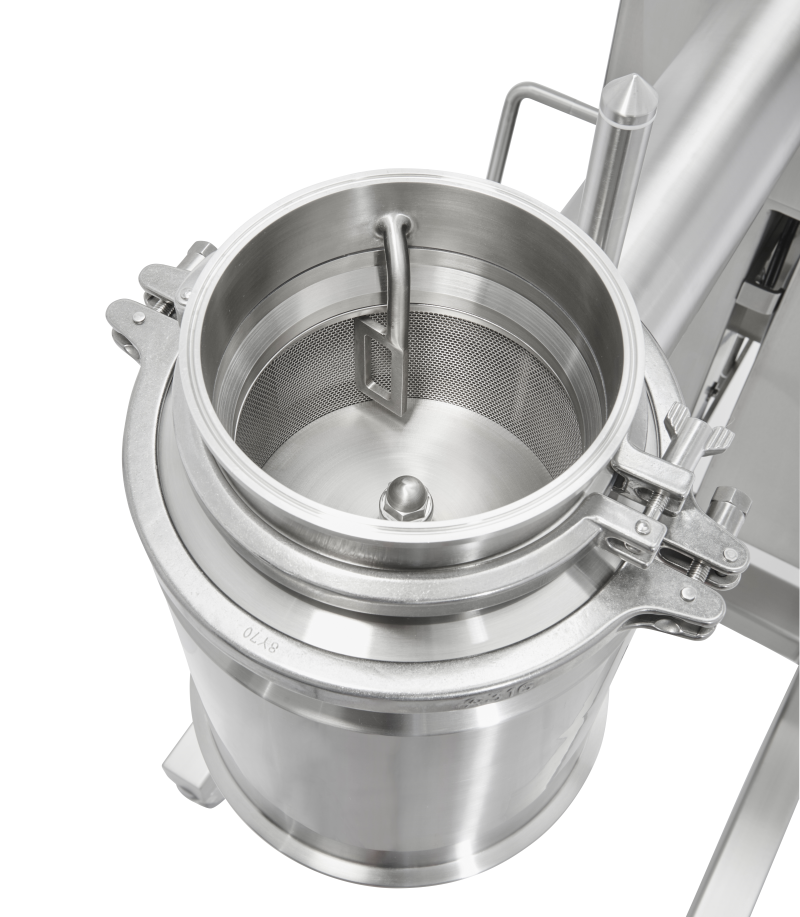
After the high-shear granulation (HSG) mixing process, where typically water or solvents are added to wet the powders, a wet mass is produced. This material is often lumpy and sticky and needs to be fed into the Fluid Bed Dryer (FBD) for the drying phase.
If the granules in the wet mass material introduced into the FBD are not of a similar size they will dry at different rates – the small particles will dry quickly, whilst the bigger lumps could remain wet at the core, which will cause problems down the line at the dry milling stage (after the FBD), where they will smear on the screen resulting in product waste and milling stoppages.
The Quadro Solution
For decades, Pharmaceutical companies worldwide have been using the Quadro® Comil® (the original conical screen mill) for removing lumps and creating granule consistency in pharmaceutical wet mass prior to the drying process.
The Quadro Comil® Underdriven Series has a compact, inline design, and short head height enabling easy integration into processing environments, and is especially useful where space is limited. A large-diameter infeed and 'straight-through' housing promote unhindered inline product flow for quicker discharge, and therefore higher throughput, improving productivity.
The Underdriven Comil® is available in various models – with model sizes designed to incorporate in-line with both lab and production-scale HSGs – thus ensuring the wet milling step is as efficient with small-scale lab or pilot systems, as it is with large production volumes. The screen type deployed will be determined by the moisture content of the wet mass. The innovative spacerless design allows for quick changeover of impellers and screens. Plus, specialized tooling is available for handling heat-sensitive products.
Learn more about Quadro's solutions for the wet milling step here.
Following the Fluid Bed Dryer (FBD) stage, the now dry material is passed through a mill once more, fine-tuning its particle size to meet the specific requirements of the manufacturing protocol. At this stage, the material is milled to ‘calibrate’ the final target particle size (PSD) – which is also known as the dry milling step.
Having achieved the correct powder condition, the pharmaceutical material is now efficiently fed to the tablet press or sachet/capsule fillers.
The Quadro Solution
Achieving an optimal particle size distribution, critical for effective tablet compaction and dissolution, hinges on leveraging the appropriate technology for dry milling.
Just like its critical presence in the wet mass conditioning step, the Quadro® Comil® is often used in the Dry Milling stage as well – thus providing a complete solution. By selecting the appropriate screens & impellers, the dry powders can be suitably calibrated according to the manufacturing objectives. Further adjustments of powder characteristics can be achieved with precise management of the equipment components:
- Tooling selection – screen hole size, shape, impeller profile
- Impeller tip speed & RPM control
- Infeed diameter, feeding method and downstream collection
Additionally, Quadro's advanced equipment ensures that products sensitive to heat are preserved throughout the milling operations, preventing degradation.
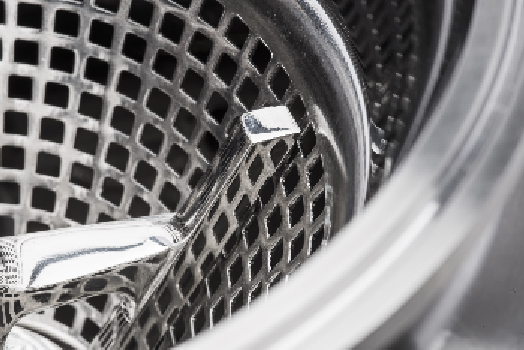
WHY US?
Quadro is the Perfect Partner for Your Pharmaceutical Milling Needs
Top-tier manufacturers are confident in Quadro for their Wet Granulation pharmaceutical milling needs. Our extensive selection of equipment is meticulously crafted to support every phase of the process - from research and laboratory work to full-scale production runs. Quadro mills are renowned for adhering to the pharmaceutical industry's most rigorous quality control and cGMP standards, ensuring reliability and excellence regardless of project size.
Understanding the critical need for product quality and operational reliability, our equipment is engineered to deliver precise results, minimize downtime and reduce waste efficiently. This operational efficiency translates into a more attractive return on investment for our customers.
As an industry leader in milling and powder processing technology, we have decades of experience helping our customers achieve success. Working closely with our customers, we ensure the equipment is set up correctly, paying close attention to the selection of the screen and impeller which can serve to reduce installation time. This attention to detail provides an added level of confidence that your powders are precisely conditioned for the OSD process, and will result in a higher-quality product batch, removing the costly risk of waste.
If you're looking for guidance on selecting the right equipment for your OSD process, our experts can help.
WATERLOO TECHNOLOGY CENTRE
Comprehensive Equipment Testing & Validation
Benefit from over seven decades of combined materials handling experience and equipment development.
The Waterloo Technology Centre offers advanced technology and equipment for testing and product development. This empowers researchers, developers, and manufacturers to conduct customized trials and feasibility tests, from lab to full production, streamlining integration and commissioning processes.
Our knowledgeable product and application specialists will be on hand to offer:
- Feasibility tests to support new product developments.
- Improvements to existing processes and/or products.
- Proof of concept for process scaling.
- Equipment trials before purchasing.
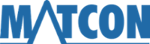
Matcon Powder Handling Systems
Complete powder and tablet handling equipment solutions for manufacturers of OSD pharmaceuticals.
Equipment for material handling, formulation, blending and powder discharge,
If you need advice and equipment for the pharmaceutical industry, speak to Matcon, another business unit of IDEX material processing technologies.
RESOURCES
Related Resources
- Blog: What Is Wet Granulation?
- Blog: Wet Granulation Step 1: Screening, Delumping & Milling
- Blog: Wet Granulation Step 2: Wet Milling & Wet Mass Delumping
- Blog: Wet Granulation Step 3: Dry Milling
- Blog: Wet Granulation With a Comil® (Conical Mill) Reduces Material Drying
- Blog: Wet Conditioning to Improve the Drying of Pharmaceutical Powders
- Blog: Dry Granulation Sizing Prior to Tableting
- Blog: Mill Powders and Granules to the Ideal Particle Size Without Heat
- Blog: Pharmaceutical Process scale-up from a Lab mill to Production